对于一辆重卡产品来说,越是看不到的地方才越能彰显内在品质。
自2022年9月第一辆梅赛德斯-奔驰Actros在国内下线以来,市场各方对奔驰卡车都给予了很高关注,但仔细梳理就会发现,大家把关注点更多集中在动力链、配置层面,却忽视了一个影响重卡品质和成本的关键因素——制造。
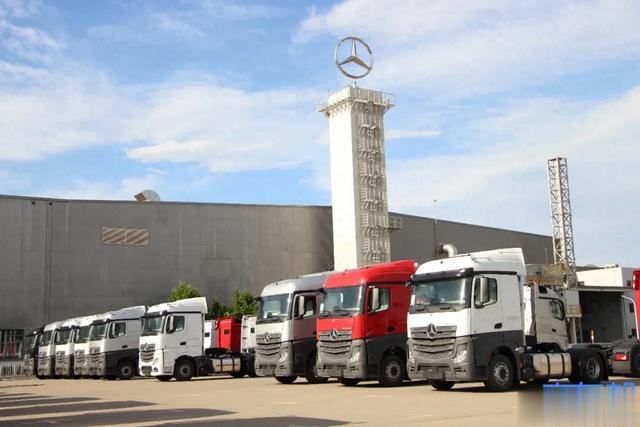
点击图片进入专属购车通道
一辆好的重卡,绝不只是高端动力链及各种花哨配置的简单堆砌,它不仅是设计出来的,更是用过硬的生产工艺和质量标准制造出来的。作为德国汽车工业的代表之一,奔驰卡车在重卡制造领域究竟拥有哪些领先优势?在我们无法直观看到的产品背后,奔驰卡车都采用了哪些独到的制造工艺与技术?它们将会给用户车辆的可靠性及全生命周期使用带来哪些直接影响?为此,商车邦独家走进奔驰卡车位于北京怀柔的制造工厂,通过深度走访交流,来立体呈现奔驰卡车高品质背后的制造实力。
商车邦
,赞46
01
焊装篇——看不到的可靠
/ NEWS
在卡车市场,可靠是经常被企业用来宣传产品的高频词,但也是让用户觉得很虚的一个词。可靠不是说出来的,而是实实在在制造出来的。在此次探访奔驰卡车在华工厂的第一站——焊装车间,当我们把一台驾驶室的几个关键生产工艺呈现出来,相信大家对可靠这个词一定会有新的认识。
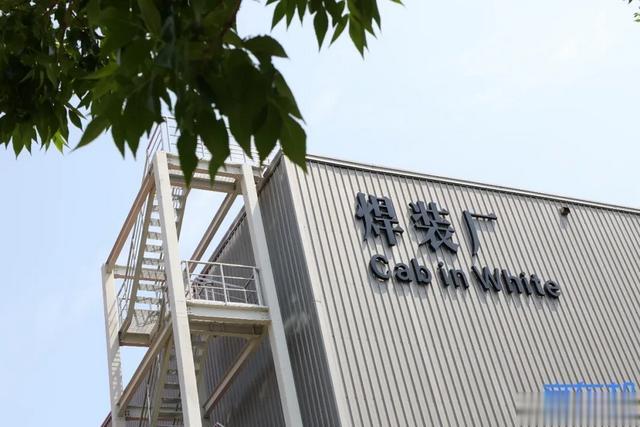
驾驶室又被称为白车身,是重卡四大核心总成之一,对整车的各项性能具有举足轻重的影响,也是重卡生产制造中投资最大、难度最高的部分。大家日常可能会更多关注驾驶室的造型和内饰,而对于隐藏在表象之下的驾驶室本体了解不多,而后者的品质在长时间使用之后才能凸显出来,也最能考验一个品牌的造车实力和造车理念。
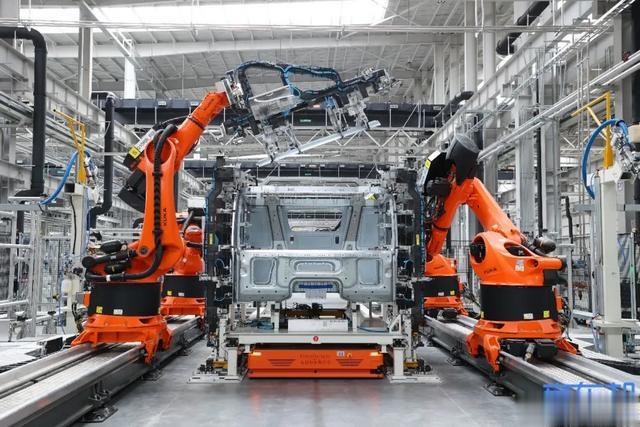
奔驰卡车焊装车间的主要工作流程就是将一辆重卡驾驶室的车身冲压单件进行定位焊接成地板、前围、后围、左右侧围、顶盖等分总成,然后再将这些分总成焊接成一个完整的驾驶室总成(因为没有涂装,也被称为白车身)。白车身就类似于毛坯房,是框架和基础,如果基础没打好,即便后期内外饰做得再好,也会影响驾驶室的整体品质。因此,焊装工艺决定了驾驶室的强度和精度,进而影响后期使用中的密封性、安全性,以及各种配置和附件的安装准确性和可靠性。而梅赛德斯-奔驰卡车焊装制造的核心优势,就体现在强度和精度的工艺保障方面。
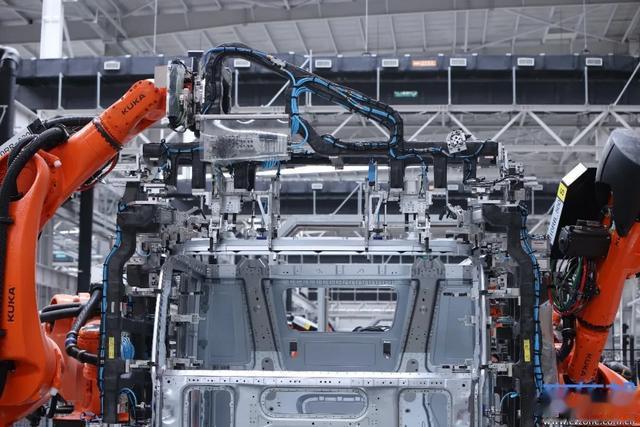
正在进行焊接作业的机器人
机器人目前在重卡行业应用越来越普遍,在智能制造中扮演着重要角色。据了解,一台奔驰卡车的驾驶室上总计有4900多个焊点。这些焊点主要由150多台机器人完成焊接,自动化率接近100%,它可以提升作业效率,消除人工差异,保证质量的一致性。在焊接作业中,焊接参数的变化将直接影响焊接质量,比如电流过大会造成击穿,电流过小会因虚焊而导致焊点开焊。由于冲压后的单件在板材厚度方面会有细微差异,焊接电流的大小就需要进行相应调整,这也是焊接工艺中的一大难点。而奔驰卡车焊装车间使用的是自适应焊枪。在焊接之前,焊枪先通过小电流来测试板料厚度及电阻值,然后根据不同的电阻值输出最合适的电流,从而保证每一个焊点的质量达到最优。
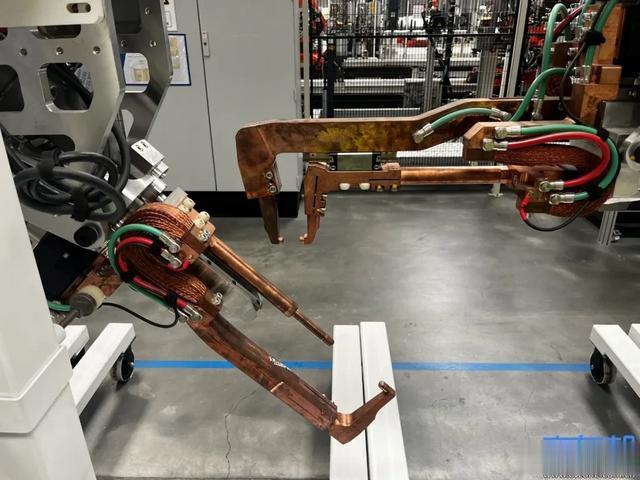
焊接机器人使用的焊枪具有自适应功能
由于驾驶室上还要安装很多附件,就需要根据安装位置在车身上焊接一些螺柱,这些螺柱的焊接质量也相当关键,如果螺柱焊接位置不准确或者不牢固,就可能会影响内饰、座椅等部件的安装精度及后期质量。奔驰卡车焊装车间对螺柱焊生产过程中的参数也会进行实时监控,一旦监测到电流等参数异常,会喷粉标示位置,并自动将缺陷反馈至后续工位展示并进行返修,以保证所有螺柱的强度。
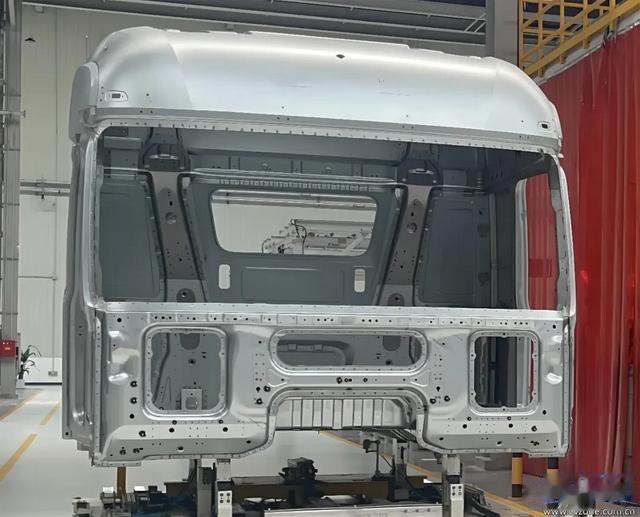
车身上有很多螺柱,其焊接质量也相当关键
焊装车间还有一项重要工作就是为白车身相关部位进行涂胶,在涂胶过程中也有全程QUISS(将视觉监测与点胶系统集成的一体化解决方案)监测,通过拍照实时监控每一段涂胶的位置、尺寸等信息,快捷地展示在屏幕上,避免驾驶室漏水、错位等质量问题的发生。
如果说焊点质量主要影响着车身强度,那么焊接精度则决定了车身的尺寸精度,进而影响驾驶室所有内饰件、外饰件能否准确安装。例如:如果白车身的侧围总成或车门总成出现尺寸偏差,就可能会影响到车门和侧围的间隙、面差以及车身的密封性。
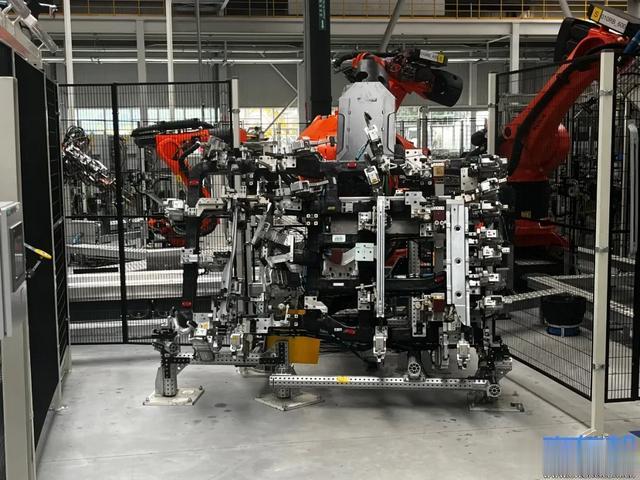
重卡制造领域首次大规模使用碳纤维材质机器人抓手
那么,如何才能提升白车身的尺寸精度呢?在奔驰卡车焊装车间,我们看到了首次在重卡制造领域大规模使用的碳纤维材质的机器人抓手(也就是工装夹具),这些抓手在奔驰卡车德国沃尔特工厂也才刚刚投入使用。碳纤维抓手会将需要焊接的零件进行精准定位,相比传统的铝和钢制夹具,它不仅重量轻,强度高,而且在长期使用过程中不容易变形,从根本上保证了焊接的精度。
人防不如技防,奔驰卡车焊装车间的防错手段已从人工转向智能化,在每个工装夹具上都配有防错用的光电检测设备,部分工位还配备拍照的设备用来确认焊接零部件的种类及位置是否准确,如果出现漏装、错装或位置不准确,设备会自动识别,停止并报警提示,不会进行下一步的动作,以确保零件的准确性及位置精度。
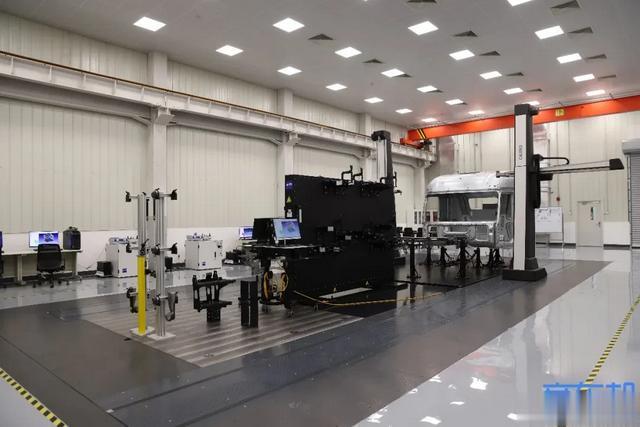

国内重卡领域首台无级调节三坐标测量仪,可以对车身各部位及孔位精度进行精准检测
商车邦
,赞29
除了我们看到的这些智能化设备和制造工艺作为质量保障之外,还有一套戴姆勒独有的质量管理体系参与到整个生产过程中。以焊装车间为例,其质量控制有四道关,称为“四环”:第一环是每个工位的工人都会对本工位进行自检;第二环是质量部在生产线设立“质量门”,对每辆车进行100%日常检查;第三环车身AUDIT检查,每一个班次抽检一台产品;第四环是整车AUDIT检测。在焊接强度方面,质量部的检查人员会每天用超声波检测设备对焊接质量进行抽样检测,并在10天之内覆盖全所有焊点;在尺寸精度方面,在每班次抽出一台产品用三坐标测量仪对车身精度进行检测,用于监控生产工艺过程的精度以及稳定性。
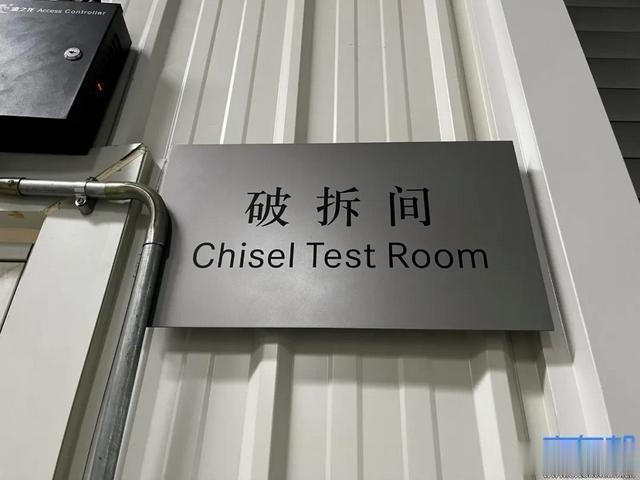

在破拆间工人用破拆工具将车身所有焊点拆开来检验每一个焊点的质量
如果你认为这些比较平常,再来给大家介绍一个“更狠”的检测方式——拆车。拆车在乘用车圈比较常见,通过拆掉车辆各种外饰件和总成件来对一款车的品质给出更有说服力的评价。而在此次参观过程中,我们看到了一个比拆车更彻底的环节,在梅赛德斯-奔驰卡车专门设有一个破拆间,里面有几名工人正在对一台下线合格的白车身驾驶室进行全破坏性拆解,通过破拆工具将所有焊点拆开,以检验每一个焊点的质量,用于检查焊接质量的稳定性。据悉,拆检的频次是每2个月抽查1台驾驶室,用时2周完成破拆。在焊点这样一个用户在商品车上根本看不到的细节,梅赛德斯-奔驰卡车在制造和质量方面的投入居然如此之大,其对于品质的态度和追求由此可见一斑。(未完待续)